ECU team competes in national robotics competition
East Carolina University’s Association of Technology, Management, and Applied Engineering robotics team took third place at the national ATMAE Conference held Nov. 2-5 in Orlando, Florida.
Led by Zack Cleghorn, an industrial engineering technology student, the team worked from August until October on the ECU robot. Other team members were David Palmieri, Oliver Chen, Cameron Coleman, Chance Smitherman, Luke Pearson, Kyle Marchand, Samuel Saunders and Josh Stevens.
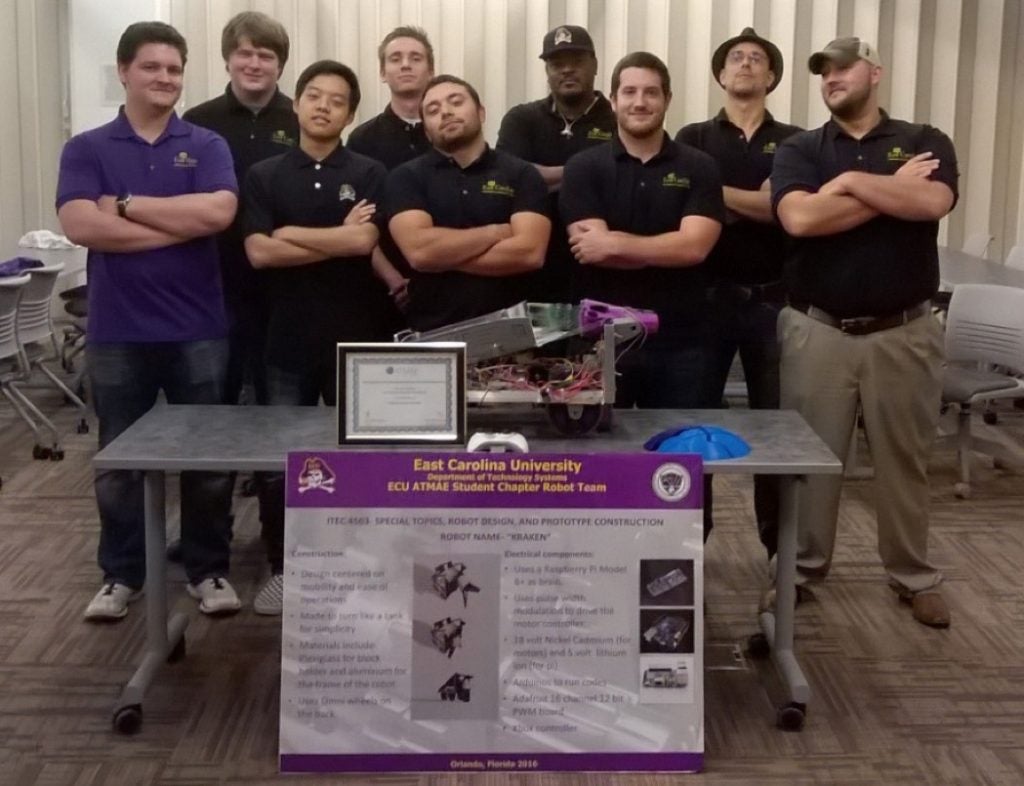
Front row (left to right): David Palmieri, Oliver Chen, Cameron Coleman, Chance Smitherman, Zack Cleghorn. Back row: Luke Pearson, Kyle Marchand, Samuel Saunders, Josh Stevens. (Contributed photo)
Faculty members Amy Frank, teaching instructor in technology systems, and Dr. Jimmy Linn, teaching assistant professor, accompanied the team made up of industrial engineering technology, computer science and technology management graduate students. It was the first time many of the students had worked on a project requiring extensive wiring, programming and design decisions.
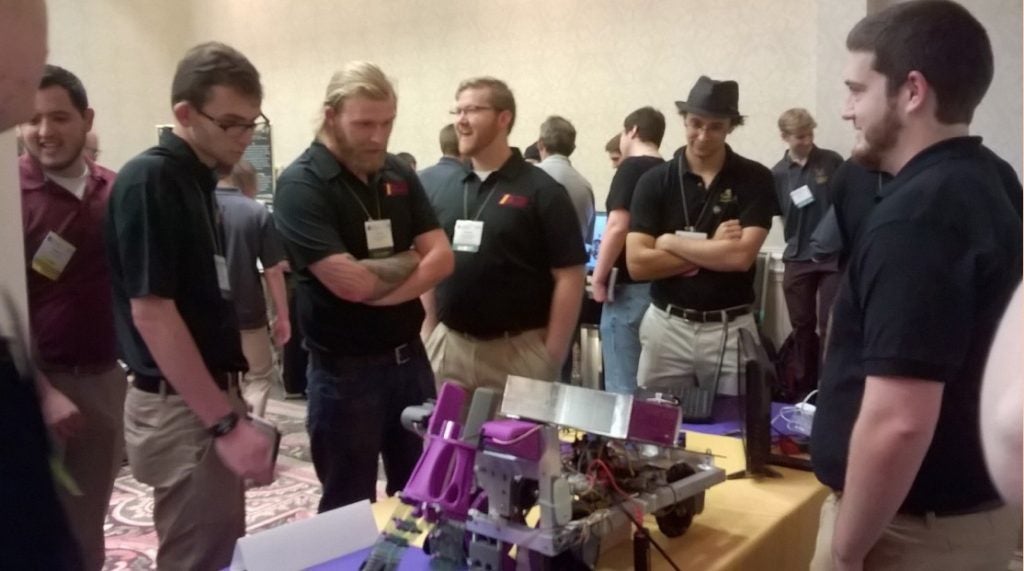
Team members from a competing team examine the ECU robot on display.
The robot had to complete two major circuits at the competition. The first consisted of a burlap bridge, a teeter totter and an automation segment where the robot had to collect five cubes and store them. The second circuit was a relay race in which the robot had to sprint down and collect irregular shaped blocks and return to the starting point. During the competition, the robot experienced a few minor automation failures over the burlap bridge, but was able to complete the teeter totter successfully for both passes.
One of the best features of the robot was its secondary inner wheels, which were 3D printed by Stevens. The wheels were adapted using riveted spokes to help pull the robot over the burlap bridge. With several infra-red sensors, an ultrasonic sensor and an Xbox controller, the robot sprang to life for the automation segment.
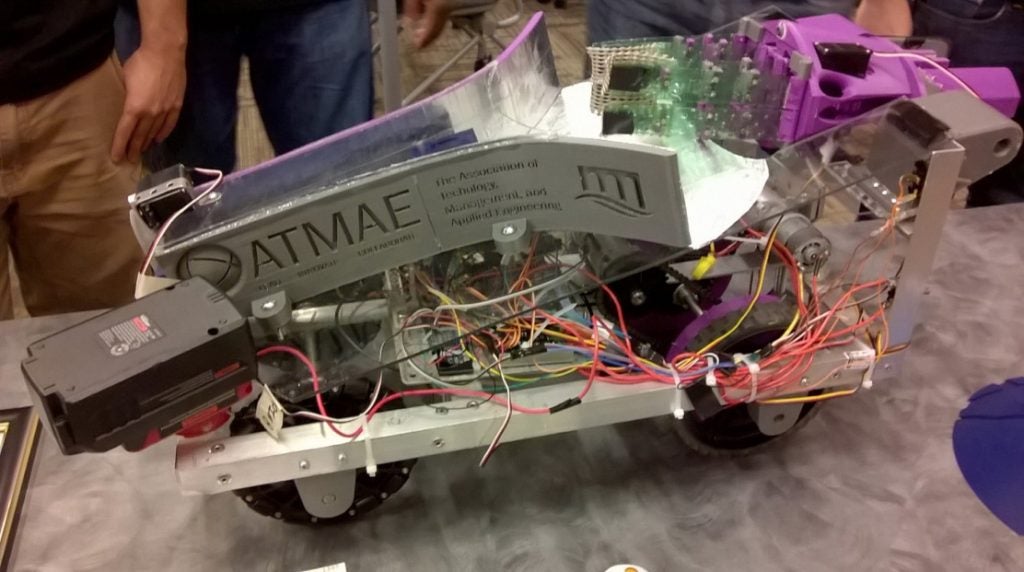
A close-up of the finished ECU robot. Several parts were made using a 3D printer.
With an aluminum frame, the robot only weighed 25 pounds.
For more information on ATMAE and the robotics team, contact Frank (franka@ecu.edu) or Linn (linnj@ecu.edu) in the Department of Technology Systems.
-by Chance Smitherman, ECU robotics team member